Forschung und Entwicklung in der LMB
Die LMB Gruppe hat mit verschiedenen Kooperationspartnern aus der Industrie und der Forschung in der Vergangenheit bereits Entwicklungsvorhaben umgesetzt und in 2024/25 zwei weitere Projekte gestartet.
Ziel dieser Projekte ist stets die Entwicklung von neuen Verfahren und technischen Ansätzen, die darauf abzielen, Produkte zu entwickeln, die danach vermarktet werden können.
Nachfolgend werden die Projekte kurz dargestellt und die Zielrichtung beschrieben:
Kurzübersicht
Anlagen- und Prozessentwicklung zur Generierung von breiten Schweißbahnen beim Laserauftragschweißen mit Multispotoptiken
Folgende Partner sind an dem Projekt beteiligt:
Team | Aufgabenbereich |
---|---|
LAT (Lehrstuhl für Laseranwendungstechnik) Ruhr-Universität Bochum | Prozessentwicklung Schweißen |
RUS(Lehrstuhl für Regelungstechnik und Systemtechnologie) Ruhr-Universität Bochum | Auslegung der Regelungstechnik und Algorithmen |
Think-Additiv Technologie GmbH | Pulverdüsenentwicklung und Prozessintegration |
LMB Automation GmbH | Optikaufbau und Maschinenkonstruktion/-aufbau |
Kamp & Kötter GmbH | Programmierung und Aufbau der Bahnsteuerung |
Förderung: OP EFRE NRW
Entwicklung einer rotierenden Bifokaloptik zum Laserschweißen
Folgende Partner sind an dem Projekt beteiligt:
Team | Aufgabenbereich |
---|---|
LAT (Lehrstuhl für Laseranwendungstechnik) Ruhr-Universität Bochum | Prozeßentwicklung Schweißen |
LMB Lasermaterialbearbeitungs GmbH | Optikaufbau |
Förderung: ZIM Projekt
Entwicklung eines Verfahrens zur Erstellung von Bipolarplatten mit nur einem Maschinenaufbau und den dazugehörigen Funktionsmodulen zur Arbeitsvorbereitung und Auswertung der Prozessdaten mittels lernender Funktionen
Folgende Partner sind an dem Projekt beteiligt:
Team | Aufgabenbereich |
---|---|
ILT (Inst. für Lasertechik Aachen) | Prozeßentwicklung Schweißen |
dLS Laser&Zerspanungstechnik | Prozeßentwicklung Schneiden |
LMB Automation GmBH | Maschinenaufbau, Aufnahmetechnik |
Förderung: ZIM Projekt
Schweißen von Kunststoff auf Kunststoff und Schweißen von Kunststoff auf Metall, jeweils umgesetzt mit einem großen Anbindungsquerschnitt.
Folgende Partner waren an dem Projekt beteiligt:
Team | Aufgabenbereich |
---|---|
LZH Laserzentrum Hannover | Prozeßentwicklung |
Sill Optics GmbH & Co. KG | Entwicklung der Optik |
LMB Automation GmbH | Aufbau Optikhalterung und Schweißkopf |
Primes GmbH | Entwicklung eines geeigneten Meßgerätes |
neoLASE GmbH | Aufbau und Ansteuerung einer Diodeneinheit |
Coherent | Unterstützung beim Aufbau einer Diodeneinheit |
VW AG | Unterstützung bei der praktischen Anwendung |
Förderung: BMBF im Rahmen KMU innovativ
Projekt BreitbahnDED
Projektübersicht: Entwicklung eines Optiksystems für breitere Pulverauftragsspuren im Laserauftragsschweißen
Die additive Fertigung mittels Laserauftragsschweißen gewinnt zunehmend an Bedeutung, insbesondere bei der Herstellung von Beschichtungen und der additiven Reparatur von Bauteilen. Ein zentraler Aspekt in der Weiterentwicklung dieser Technologie ist die Erhöhung der Prozessgeschwindigkeit bei gleichzeitig hoher Qualität des Materialauftrags. Eine vielversprechende Möglichkeit zur Effizienzsteigerung besteht darin, breitere Schweißbahnen zu erzeugen. Dies erfordert jedoch angepasste Systemkomponenten, insbesondere im Bereich der Laseroptik und Pulverzufuhr.
Im Rahmen des vorliegenden Projekts wird ein Optiksystem entwickelt, das auf breitere Pulverauftragsspuren ausgelegt ist. Ziel ist es, durch technische Optimierungen eine höhere Auftragsrate zu erzielen und gleichzeitig die Prozessstabilität sicherzustellen. Die LMBA übernimmt dabei zwei zentrale Arbeitspakete: die Entwicklung eines geeigneten Optiksystems sowie den Aufbau einer funktionsfähigen Workstation für die Durchführung der Beschichtungsprozesse.
Projektziel
Im Rahmen des Projekts soll ein Verfahren zur Erzeugung breiterer Schweißbahnen im Pulverauftragsschweißen entwickelt werden, um den Materialauftrag effizienter zu gestalten. Da herkömmliche Standardoptiken nur begrenzte Möglichkeiten zur Vergrößerung des Fokusdurchmessers bieten, ist der Einsatz spezieller Optiksysteme erforderlich.
Arbeitspaket 1: Entwicklung eines Optiksystems
Die erste Aufgabe der LMBA besteht in der Entwicklung einer Optik auf Basis einer Drehoptik, mit der sich breitere Pulverspuren erzeugen lassen. Zu diesem Zweck werden verschiedene Optiken ausgewählt und in einen standardisierten Versuchsaufbau integriert. Die erforderliche Pulverdüse wird durch einen Projektpartner bereitgestellt und muss in enger Abstimmung mit der Optik angepasst werden. Ziel ist es, die Pulverzufuhr und die Laserstrahlform optimal aufeinander abzustimmen, um gleichmäßige und reproduzierbare Auftragsbahnen zu ermöglichen.
Arbeitspaket 2: Aufbau einer Beschichtungs-Workstation
Die zweite Aufgabe umfasst den Aufbau einer geeigneten Workstation für die Durchführung der Beschichtungsprozesse. Dabei liegt ein besonderer Fokus auf dem Schutz der mechanischen und optischen Komponenten vor Pulverpartikeln. Es sind unter anderem folgende Maßnahmen vorgesehen:
- Einsatz pulverdichter Linearführungen
- Integration pulverdichter Optiken
- Aufbau eines geschlossenen, pulverdichten Gehäuses mit entsprechender Absaugtechnik
Die Steuerung der Anlage wird von einem Projektpartner bereitgestellt und liegt außerhalb des Aufgabenbereichs der LMBA. Eine enge Abstimmung mit diesem Partner ist jedoch erforderlich, um eine reibungslose Integration aller Systemkomponenten zu gewährleisten.
Projekt TwinWeld
Mit dem Laser lassen sich sowohl Werkstoffe mit hoher Schmelztemperatur als auch mit hoher Wärmeleitfähigkeit schweißen. Aufgrund der kleinen Schmelze und der kurzen, steuerbaren Schmelzdauer können sogar Werkstoffe verbunden werden, die sonst nicht schweißbar sind.
Bei Bedarf können Zusatzwerkstoffe in Form von Draht, Pulver oder Paste verwendet werden.
Dennoch gibt es beim Laserschweißen von Metallen immer noch zahlreiche wiederkehrende Probleme, die die Qualität einer Schweißnaht negativ beeinflussen können.
Folgende Aspekte sind beim Laserschweißen von metallischen Werkstoffen zu beachten
- Eine gute Vermischung
- Gute Verbindungen zur Wärmeeinflusszone
- Gleichmäßige Wärmeeinbringung über den gesamten Bereich, keine Abflachung der Leistungsdichte zur Nahtkante
- Anpassung an unterschiedliche Spaltbreiten
- Anpassung an unterschiedliche Nahtbreiten
- Reduzierung von Ungänzen/Poren vor allem im oberen Nahtbereich
- Verbesserung der Oberflächenstruktur
- Verbesserung der Schweißnähte bei Einsatz von Al-Druckgußqualitäten
Ziel des geplanten FuE-Projektes ist die Entwicklung eines neuartigen Schweißkopfes mit zugehöriger Prozessführung für das effiziente Laserschweißen unter der Verwendung schnell rotierender Fokuspunkte. Damit soll ein definiertes Temperaturfeld innerhalb der Fügezone erzeugt und die Strömungsdynamik innerhalb des Schmelzbades gezielt beeinflusst werden. Das eingesetzte bifokal rotatorische Schweißverfahren nutzt die Aufspaltung des eingekoppelten Laserstrahls in zwei Teilstrahlen. Mittels geeigneter opto-mechanischer Elemente werden die Teilstrahlen in eine schnelle Rotationsbewegung gebracht. Durch eine Relativbewegung dieser rotatorischen Bewegung entlang einer Kontur auf dem zu schweißenden Bauteil (Vorschub in der Schweißung) wird durch eine Überlagerung beider Bewegungskomponenten eine Vermischung, eine Art „Wobbel-Bewegung“ erzeugt.
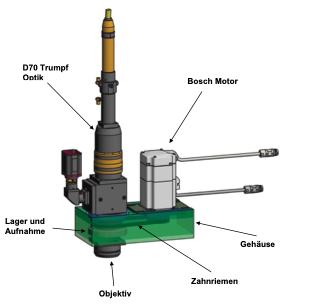
Projekt Brennstoffzelle
Das Ziel dieses Projektes ist die Entwicklung einer Anlagentechnologie mit den zugehörigen Fertigungsprozessen für die vorserielle Produktion von Bipolarplatten, die zur Herstellung von Brennstoffzellen benötigt werden. Die Anlagentechnik soll dabei die Fertigungsschritte des Schweißens und des Schneidens kombinieren, um somit eine Erhöhung der Produktivität zu erzielen. Weiterhin soll mit dieser Anlagentechnik die benötigten schichtweise aufgebauten Spannvorrichtungen erstellt werden.
Durch die zusätzliche Digitalisierung der Anlagentechnik mit Lernprozessen aus den einzelnen Abläufen sollen somit Spannelemente, Prozessparameter und Schweiß- bzw. Schneidreihenfolge angepasst und optimiert werden, um den Ausschuss in der Vorserienproduktion zu reduzieren. Zusammenfassend lassen sich mit dem geplanten Fördervorhaben folgende Vorteile erzielen:
- Aufbau einer Anlage, die die Aufgabenstellungen Schweißen und Schneiden bei der Bearbeitung von Bipolarplatten in einem Aufbau abdeckt
- Erhöhung der Anlagenauslastung durch Kombination von Schneid- und Schweißprozessen
- Herstellung von schichtweise aufgebauten Spannvorrichtungen durch die Anlagentechnik
- Optimierung der Prozessparameter, Schweiß- bzw. Schneidreihenfolge und Spannvorrichtung durch integrierte Lernprozesse
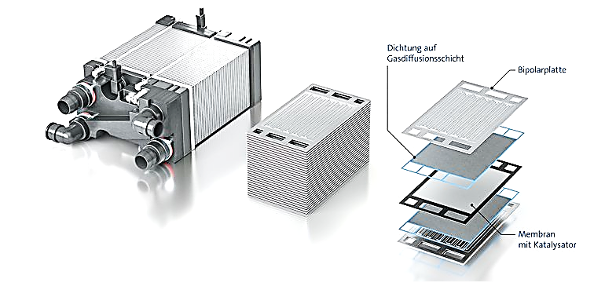
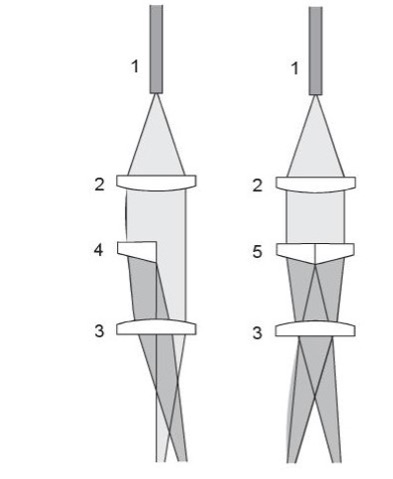
1: Laserlichtkabel, 2: Kollimator, 3: Objektiv, 4: Quarzglaskeil, Doppelkeil.
Projekt Multispot
Bei Multispot geht es um das Kunststofffügen mit großen Anbindungsquerschnitten mittels einer Multifokal-Laseroptik. Mit einem neu entwickelten Schweißkopf, bei dem mit einer Matrix von 3 x 3 Laserspots gearbeitet wird, kann Kunststoff mit Kunststoff und Kunststoff mit Metall großflächig miteinander verbunden werden. Das Equipment und der Prozeß wurden gemeinsam mit einem Institut, vier Unternehmen und zwei assoziierten Partnern durchgeführt. Neben schmalen Schweißnähten werden mehr und mehr breite Schweißnähte benötigt, um die geforderte Festigkeit und Dichtheit zu erreichen. Zur Umsetzung ist ein großer Laserspot notwendig, den man mit einer einzelnen Optik nicht erreichen kann. Der Einsatz eines Scanners ist ebenfalls nicht geeignet, da bei einem großen Anbindungsquerschnitt mit dem Scanner die gesamte Fläche nicht gleichzeitig sondern nur punktuell nacheinander erwärmt wird. Bei Einsatz eines großen Arbeitspunktes wird die Energie mit einer konstanten Intensitätsverteilung in das Werkstück eingebracht werden. Dies ist nachteilig beim Schweißen von Konturen; denn beim Abfahren von Kurven wird im äußeren Bereich zu wenig und im inneren Bereich zu viel Energie eingebracht. Dies kann mit der Multispotoptik angepasst werden
Aufgebaut wurde eine Optik, bestehend aus 9 Einzeloptiken, die in einer Matrix von 3 x 3 angeordnet werden. Jede einzelne Optik wird über eine separate Diode versorgt, die einzeln angesteuert und reguliert werden kann. Damit lässt sich das Profil der Strahlverteilung beliebig einstellen. Beim Aufbau der Optik lag die Problematik darin, mit den neun Optiken eine gleichmäßige Energieverteilung in der Fläche zu erreichen. Dies wurde erreicht, wobei der Aufwand nicht unerheblich war. Mit einem geringeren Aufwand konnte eine Verteilung erreicht werden, die wirtschaftlich umsetzbar ist.
Eine zweite Anwendung für das Schweißen mit einer breiten Naht ist das Verschweißen von Kunststoff mit Stahl. Um hier die geforderten Festigkeiten zu erreichen ist ein großer Anbindungsquerschnitt notwendig. Bei den Versuchen hat sich herausgestellt, dass die geforderte Festigkeit nur erreicht wird, wenn das Blech an der Schweißstelle aufgeraut wird. Gemeinsam mit dem LZH wurde zusätzlich ein Konzept entwickelt, um die Optik zusammen mit einem Roboter einsetzen zu können. Aufgebaut wurde ein voll funktionierender Demonstrator, mit dem Anfang 2023 Vorführungen gestartet werden.
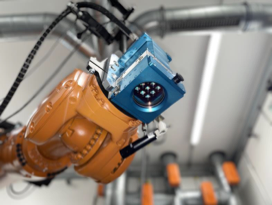
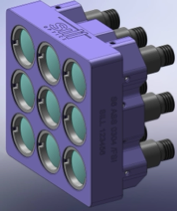
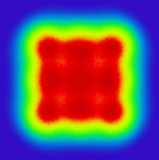
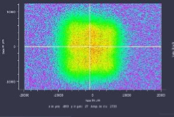